The smart factory has the potential to reinforce labor productivity threefold over the next decade. Deloitte reports. digitalization of manufacturing is gaining momentum by incorporating fast-moving technologies such as industrial IoT, big data analytics, cloud environment, M2M communication (machine to machine), artificial intelligence, and machine learning.
Industry 4.0 may turn out to be challenging for those businesses that lag behind in terms of adapting to new realities impacted by the IIoT acceleration. By combining advanced digital technologies, the manufacturing industry is able to converge the digital and physical worlds through the unprecedented value of insights across the supply chain lifecycle.
Let’s get into detail and shed light on each technology capable of optimizing operations, processes, and assets.
What Is a Smart Factory?
It is worth noting that a smart factory can be substituted by the following synonyms: intelligent manufacturing, industrial Internet of Things (more about its underlying concept), Industry 4.0., and digital factory. All these word combinations denote full-fledged automated, digitized, and IoT-driven solutions aiming at collecting production data, analyzing it to bring actionable insights, and augmenting human intelligence through machine learning algorithms to ensure flexible, efficient, and streamlined processes at each step of the manufacturing lifecycle.
To achieve the ultimate goal of a holistic view of the processes, the production activities are backed by IIoT (Industrial Internet of Things). Let’s move forward and outline the benefits and applications, and how actually your business can be impacted by the IoT, cloud computing, and big data analytics.
What Is IIoT? Why Do Businesses Procrastinate Implementing It?
Industrial IoT is the way how manufacturing can optimize its efficiency by connecting critical assets, sensors, devices, machines, and robots. It is aimed at streamlining operational efficiency by collecting and tracking data in real time to generate actionable insights. They can help identify scenarios to enhance manufacturing processes and facilitate faster and more accurate decision-making.
To better understand the specifics, let’s overview such a use case. By installing IoT sensors (for example, those being able to check humidity or temperature levels) on the products that are transported from one point to another, manufacturers can get complete visibility of the products’ states. By remotely monitoring and tracking the conditions and the performance of assets, managers can be certain that proper storing conditions are provided and damages are prevented.
However, realizing the potential of the smart factory to reinforce operations, manufacturers are still hesitating to jump on this train without estimating the values they can gain and how their existing operations can be scaled and accelerated by IIoT. Indeed. This is one of the most widespread mistakes of organizations that do not know how to set proper priorities. This results in bold investments and time wastes. Therefore, its important to evaluate the possibilities IoT technologies can generate considering the customers’ demands and current business models in your organization.
According to McKinsey & Company research, there are six myths businesses believe in that constrain them from embracing the Industrial Internet of Things. We analyzed them and outlined the main myths and obstacles of IIoT adoption and recommend the solutions to overcome them:
- IIoT will eliminate people’s demand. People will be always required, especially in the digitalization of business processes. The thing is that along with displacing jobs that are focused on doing repetitive and tedious tasks, the smart factory provides new jobs that require gaining new capabilities. This, in turn, requires reskilling of the staff to make the most out of advanced technologies. But with huge leaps forward, there is no way back to your workforce to not acquire new capabilities.
- IIoT requires total readiness. Prolonged time planning can turn out to be totally ineffective. Following Agile methods, businesses learn fast from failures since this approach allows them to facilitate rapid development and continuously improve by quick iteration in one-week sprints.
- Upgrading is not cost-effective. On the contrary, the IoT market is flourishing thanks to the connected sensors’ drop in prices. Based on the experience of many businesses, the adoption of smart technologies results in cost reimbursement. And here we debunk the following myth about the infeasibility of IIoT for old equipment: you can optimize your existing infrastructure with a minimal substitution of the equipment or even without the need to replace it. The main pillar for coming into smart factory technology is an augmentation of the existing systems by IoT-powered sensors, devices, and applications that are capable of managing and controlling the bulk of the endeavor. Moreover, predictive maintenance can significantly eliminate downtimes and reduce maintenance costs by up to 40 percent.
Leverage Smart Manufacturing Technologies to Stay Ahead: IIoT Benefits to Embrace
Real-time monitoring and asset management
To monitor the most valuable assets in real time and efficiently manage the manufacturing processes, industrial businesses can connect them and get a complete view of all the stages throughout the production lifecycle. All this is possible by implementing asset tracking systems and smart devices and sensors that are installed into assets in manufacturing production, supply chain, and logistics. Being interconnected, manufacturers and managers will get data on a granular level. The latter will be transformed into meaningful insights in the centralized system where data sets are not siloed. Therefore, the whole production cycle is fully controlled and optimized thanks to automatic reporting, real-time alerts, and enhanced monitoring maintenance.
With sensor-equipped machinery, the factory has the potential to facilitate the visibility of physical assets throughout the working environment. Sensors collect asset-tracking data that is comprehensive and accurate. This impacts the enhancement of control, business strategic decisions, and inventory reporting.
Example: AWS IIoT solutions allow businesses to optimize the quality of the manufacturing outcomes, maximize the assets’ usage, and detect potential malfunctions beforehand. All these use cases can be achieved with the incorporation of cloud computing technologies, advanced analytics, and IoT.
Streamlined Business Operations
When data is tracked in real-time, asset utilization is optimized and automatically maintained. That means the equipment is continuously controlled and can be adjusted automatically. This helps manufacturers streamline their functions. With IoT-enabled data systems, the volume of inventory operations is reduced due to remote monitoring of critical assets. This, in turn, diminishes the manual involvement of employees whose efforts can be more valuable for strategic business decisions.
Streamlined business processes mean fewer errors, fewer spare parts, and downtime, enhanced quality control, and employees’ improved productivity. With such maximized efficiencies, businesses can increase their ROI and boost their profits. The main rule here is to estimate your current state of legacy systems and identify what data points have to be captured and analyzed.
Asset downtime prevention with predictive maintenance
According to Deloitte, poor maintenance strategies affect unplanned downtime, which, in turn, deteriorates manufacturing productivity, user experience, and revenue. This costs businesses $50 billion annually. There is a dilemma relating to the maximization of asset availability. Businesses tend to have a trade-off problem: whether to run machines until they fail or replace potentially good parts beforehand. Utilizing data from various touchpoints (sensors, ERP, CRM, and other maintenance management systems) combined with ML, predictive maintenance (PdM) represents a huge potential for factories. They can accurately predict failures and prevent them in advance.
Traditional preventative maintenance, as opposed to predictive maintenance, involves the number of people spending hours on the routine manual collection and permanent analysis of equipment pieces the results of which may turn out to be inaccurate. Predictive maintenance comes into play to struggle with unplanned downtime by providing real-time insights into equipment operations and ensuring that all assets are utilized in a most efficient and effective manner. What does the process look like? Data obtained from temperature, vibration, humidity, etc. sensors are transformed into digital signals to further be processed and analyzed. Afterward, with advanced analytics and predictive maintenance algorithms, those signals are transformed into visualized insights on the dashboards (with the usage of API) on the computers or apps on smartphones. Then they are turned back into physical actions in the form of maintenance alerts.
Example: Bosch Nexeed, the connected factory located in Blaichach, integrates production and logistics processes by implementing smart software allowing it to retrieve data from 60K sensors and deliver it in real-time to the Kunz system. With a performance tracking system, the data is instantly accessible among all machine operators, making the manufacturing processes accurately estimated and improved accordingly. Subsequently, the operators are able to detect malfunctions at the earliest stages and prevent deviations proactively to minimize machine downtime. The results are baked by statistics: productivity is increased by up to 25% and inventories are reduced by 30%. Moreover, in terms of sustainability, the plant consumes 40% less power thanks to the compressed air system.
Enhanced Labor Management with Smart Robotics
Smart robots denote an AI system that can collect and analyze data from the environment and apply it to make more progressive outcomes than humans. With strong capabilities to learn and percept, smart robots can not only manage repetitive tasks but in collaboration with humans generate advanced business-critical decisions based on previous experience and learning models. Incorporating IoT sensors and machine learning algorithms in smart robotics allows manufacturers to improve supply chain and logistics.
One of the smart factory technologies deploying smart robotics is autonomous guided vehicles (AGV). They can significantly accelerate logistics processes around the factory floor by taking over heavy lifting, which positively impacts employees’ productivity and safety.
Example: TRUMPF Group, an industrial machine manufacturing company, deployed AGV lift trucks to automate materials’ moving processes. The solution accelerated the workforce efforts by saving time for skilled production operators and focusing them on more business-critical processes. As you scroll back to the section regarding the myths of smart factory implementation, particularly about the humans’ displacement on the manufacturing sites, you can now debunk them by yourself by checking out the next AGV examples.
Digital Twins
Digital twins are digital replicas of any real-world physical objects, business processes, places, people, and even cities. IoT, real-time data, simulation, and machine learning technologies are used to create virtual representations that facilitate the accurate and innovative prediction of the future of any connected environment. A digital twin can be applied, for example, in a machine engine or wind turbine that is equipped with IoT sensors, software analytics, and artificial intelligence. Using real-world data, a digital twin creates simulations represented in the digital copy, which is then applied to the original physical object or process to predict how they will perform.
For example, you need to collect all critical engineering data about the automobile engine such as energy use, temperature, air conditions, etc. IoT sensors will capture all these parameters to create a digital copy to gather insights into performance and make appropriate product refinements or take other measures, ensuring greater manufacturing efficiency.
Example: Siemens Elektronikwerk Plant, outfitted with AI, Industrial Edge Computing, cloud technologies, collaborative lightweight robots, and 3D printing, increased its production thirteen-fold since 1991. With digital twins of the product, Siemens’ team managed to decrease the production of the Simatic controller components from 11 to 8 seconds of cycle time. In addition, digital twin technology is applied to identify sources of failure in production by testing and optimizing the elements beforehand. Real-time monitoring systems allow for capturing operational data that feeds the digital twins of performance to prevent downtime and maximize efficient energy usage by applying predictive maintenance.
How to Build Your Smart Factory: Guidelines
We outlined the main guidelines to follow before stepping on the pathway of smart manufacturing technologies.
- Determine your business goals and objectives. By identifying your priorities and pain points, you can go further with investing in outfitting your current equipment with connected technologies. In this phase, it is essential to establish the digital culture in your company by incorporating a digital strategy of orchestrating people and machines.
- Develop an Industry 4.0 roadmap. When starting elaboration, you must outline the existing issues that need to be addressed first and then move further. With that in mind, start working on the milestones beginning from the components and machines of a single site and ending with the digital integration of the whole ecosystem.
- Establish IoT connectivity. There are several areas that need to be covered here:
- Network infrastructure. You have to determine what network infrastructure you want to build taking into account your existing infrastructure, the potential generation of the data volume, and criteria such as scalability, costs, security, maintenance, etc. You have three options: on-premises (local servers), dedicated cloud platform, or hybrid infrastructure.
- Wireless connections. Physical assets and operations across the factory have to be connected to enable manufacturers to obtain a holistic view from multiple data sources. To build an IIoT stack system, there should be considered the following aspects: hardware, IoT sensors, communication protocols enabling data transportation between sensors and devices, IoT platform (getaway, data ingestion, data lake), data visualization, and control.
- Integrate systems. To solve the challenges of data security, interoperability, and scalability, IT (information) systems and OT (operation) systems have to be seamlessly integrated. Enterprise Business Applications (ERP, SCM, PLM, etc.), Manufacturing Operation Management apps, and Industrial Automation apps have to be connected to each other to ensure the smooth and holistic flow of production processes.
- Harness advanced analytics. To make data-driven decisions, big data has to be categorized, cleansed, and structured in a manner allowing to sift it into actionable insights. With data analytics, manufacturers can diminish deviations and get appropriate alerts and reports based on asset monitoring and predictive maintenance algorithms.
Ready to Get Started?
To embark on the digital transformation of your manufacturing processes, it is not enough to embrace connected technologies. It’s a step-by-step strategy that starts with identifying your critical areas for data-driven upgrading.
First, you need to estimate your legacy systems and how they can be integrated with Industrial IoT-powered systems. Furthermore, determine assets that are of high priority to be monitored and controlled. Afterward, proceed with the connectivity network architecture to make this transition smooth and seamless.
If you hesitate or need profound details on how to start your digital transformation path, let us know and we will gladly discuss your project to offer you a customized solution.
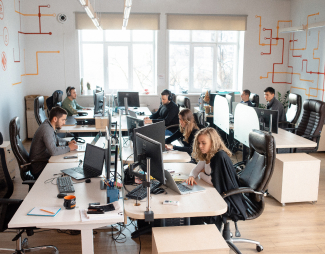
Our Engineers
Can Help
Are you ready to discover all benefits of running a business in the digital era?
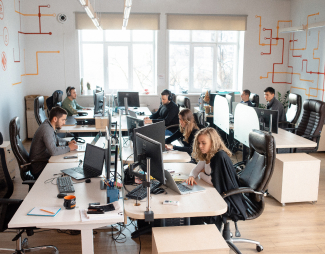
Our Engineers
Can Help
Are you ready to discover all benefits of running a business in the digital era?