Any entrepreneur of today knows how numerous the sole basics of successful business in the 21st century are. You must find your niche, identify the target audience, have high-profile goods to offer, expand your product line, train personnel, manage orders, provide adequate customer support, and do dozens of other things that will enable you to build a thriving company.
Besides, there are some fine points to mind that are peculiar to each industry. And if it is retail, inventory management techniques are one of the cornerstones that ultimately determine the vibrant performance of your organization.
What Is Inventory Management?
Inventory management, also known as store inventory control, is an element of supply chain management that boils down to tracking the movement of products from one endpoint to another.
What is the picture that comes to your mind when you hear the phrase “stock inventory”? Chances are, you think of a warehouse storing an assortment of goods to be delivered to rightful end consumers (or to vendors who will further sell them wholesale or retail). Being generally true, this vision omits a few essential details.
First of all, Industry 4.0 has ushered a line of intangible products (like software), so IT inventory management, for instance, deals with virtual merchandise located in digital depots only. Second of all, inventory planning and tracking embrace not only finished products waiting in a warehouse to be sped to the consumer. Other items included in the broad category of inventory are:
- Raw materials that the manufacturer uses to produce its output;
- Decoupling inventory which encompasses those raw materials that serve as an emergency stock to prevent any downtime in manufacturing;
- Unfinished products which aren’t ready to be sold yet;
- In-transit goods which are no longer in the warehouse but are being shipped to their destination;
- MRO (maintenance, repair, operating) goods that cover supplies needed for an uninterrupted production cycle;
- Buffer inventory with a safety stock of depleted products kept in case a sudden spike in demand or supply chain suspension occurs;
- Anticipation inventory, which consists of items kept in the stock that may be needed to satisfy customers’ demands during a certain event or season (like candy and cards for St. Valentine’s Day or warm clothes for winter).
Before choosing inventory tracking methods that will allow you to efficiently manage any kinds of goods listed above, you should have a clear understanding of the entire procedure of product movement and control.
Inventory Management Process in Detail
The whole algorithm seems quite natural and foolproof, so some entrepreneurs (in fact, as much as 43% of small businesses) may wonder if they even need to bother about any inventory control methods. Indeed, what can go wrong?
The first possible pitfall is understocking. You may underestimate the number of raw materials or MRO products necessary for a seamless workflow. As a result, your company’s operations will be suspended indefinitely. You will lose precious time waiting for the necessary items to be delivered, and downtime is always about the loss of revenues. If your miscalculations involve finished products, your clients will give you a piece of their mind as to the quality of service at your organization and its reliability as a business partner.
The second problem is the opposite – overstocking. If you manufactured more items than customers need just now, additional storage space must be found for them, which involves an increase in related expenses. Besides, if those goods are flowers or foodstuffs, they can’t sit on the shelves for long even under the best storage conditions. And losing them spells financial damage again.
Now you do see the inventory management importance, don’t you? By leveraging proper types of inventory strategies and applying adequate inventory control techniques, you will be able to improve cash flow, minimize expenditure related to mis-shipments, out-of-stocks, spoilage, overstocks, etc., and enhance the efficiency of your business in general.
Inventory Management Techniques
What are the most popular techniques applied in inventory management?
Economic Order Quantity (EOQ)
This formula takes into account a set of variables (demand rate, order cost per purchase order, and annual holding costs per unit) to identify the optimal number of products to be bought and thus rule out overstocking.
Minimum Order Quantity (MOQ)
While the previous number is supposed to watch for excessive supply, this one is called to determine the smallest quantity of goods that will keep the business going.
ABC Analysis
As the name hints, the technique divides goods into three categories (A, B, and C) depending on their impact on the overall inventory cost. The first group includes the most valuable products that give the most profit. The third group comprises items whose significance is the smallest. Group B consists of products that cover the middle ground between A and C in terms of profitability.
Just-in-Time Inventory Management
This inventory control method is used to receive products on demand when they are needed instead of receiving them in excess and risking some part of them turning into dead stock.
Safety Stock Inventory
It runs contrary to the previous method because it consists in ordering extra inventory just in case. Although leading to certain additional expenditures, it safeguards the company against stock-outs that may happen due to imprecise forecasting, unexpected fluctuations in demand, or supply chain disruptions.
FIFO and LIFO
These two acronyms stand for first-in, first-out, and last-in, first-out correspondingly. As it is quite easy to guess, FIFO presupposes selling older inventory first to keep the stock fresh. The second method means selling the last delivered item first. LIFO is typically leveraged for big-ticket items (like cars) to save on tax payments. The most recent products to arrive are conventionally costlier, which means lower net and taxable income to be filed.
Six Sigma and Lean Six Sigma
The Greek letter sigma in the assessment of the quality of manufacturing is used to denote a deviation from the standard. There are six indices that represent six standard deviations. They can be applied in inventory management to ensure the delivery of defect-free products in the stipulated time. The lean six sigma technique combines this methodology with the principles of lean enterprise, enabling companies to eliminate eight kinds of waste and thus reduce expenditure.
Reorder Point Formula
This indicator triggers the ordering of goods when a minimum threshold of items available at the warehouse is reached. To make allowance for the lead time, this number should somewhat exceed the safety stock index.
Batch Tracking
When you can group similar items to monitor their vital parameters (like expiry date) or trace the defective ones to their original batch, inventory handling is remarkably streamlined and accelerated.
Bulk Shipments
This is another scheme of dealing with items in bunches. Naturally, once you can afford to stack up a bulk of products for a single shipment, the delivery will cost much less.
Consignment Inventory
As you can guess, this approach is employed for the consignment business model in which the wholesaler allows the retailer to pay for the obtained inventory only after it is sold. Technically, the wholesaler still owns the goods and is ready to wait for the money from the vendor without any upfront payment.
Perpetual Inventory Management
This is one of the classical methods of inventory control when items are registered (either manually or by using barcode and RFID devices) as soon as they arrive. In this way, you can monitor your inventory in real time and see its movements 24/7.
Dropshipping
It is a perfect scheme if you want to get rid of the storage headache. Instead of keeping inventory at your facilities, you buy the item on demand from a third party (that will defray all warehouse maintenance expenditures) and deliver it to the customer.
Cross-Docking
Alternatively, you can apply this warehouse-free method when products are reloaded from one vehicle directly into the other. In addition to cost-saving, cross-docking facilitates the speed of delivery, which is crucial for perishable goods.
Demand Forecasting
Having historical data on purchases, you can predict the demand and plan supply delivery in advance. All these techniques will work well if you reinforce them with the life hacks we would like to offer.
Inventory Management Tips to Heed
What else should you do while mapping out your inventory management strategies?
1. Come to Grips with Your Supply Chain
Since inventory management is only one cog in the supply chain mechanism, you should have a clear vision of the whole cycle. It means detailed information on all stakeholders and business partners (your supplier, the logistics company that delivers goods, customers you sell your products to, banks you cooperate with, etc.). When you have all their merits and demerits at your fingertips, you will be able to make data-driven decisions as to each element in the supply chain.
2. Monitor Sales
It is not just calculating what is sold at the end of the day. You should find out what items are sold more often than others and why. Is it because of seasonal tides and ebbs? Is it because of their quality? Do some items always accompany each other in sales? In this way, you will have a deeper understanding of consumer habits and will be able to forecast future developments in your niche.
3. Track Product Data
All information about each product (origin, manufacturer, price, supplier, barcode, SKU, etc.) should be entered into your records and updated in case it changes. Special attention should be paid to parameters liable to shifting (such as price) to determine the pattern of changes and figure out possible reasons for fluctuations (for instance, seasonality or scarcity).
4. Audit Your Inventory
Make it a rule to perform a headcount of your inventory at certain intervals. Instead of assuming what you have by doing simple addition to and subtraction from the previous numbers, get the true-to-life picture of your assets. You will be surprised to discover how many ghost items there are in your records. There are surely products lurking on your back shelves being unaccounted for in the database. And you may still be easily selling them at your own expense. Besides, some inventory items might appear to be damaged, broken, or unusable. As a result, such roll-calls will help fine-tune EOQ, MOQ, and other mission-critical indices.
5. Ditch Slow-Moving Products
Some items may sit on the shelves indefinitely, eating up your storage space and tying up your finances that could be better directed elsewhere. The audit procedure will enable you to identify such products and get rid of them.
6. Employ Inventory Management Software
With such a scope of inventory control tasks and the slew of techniques used to solve them, it is obvious that you can’t do it manually. To achieve effective inventory management, you have no choice but to harness specialized software. The seasoned team of high-profile IT experts at Forbytes can develop a custom inventory management solution of any complexity that will impress you with a broad range of features, seamless functioning, and a moderate price.
Drawing a Bottomline
Today, one can’t build a successful business without having a robust inventory management policy in place. By employing specialized solutions to track the movement of your products, you will streamline the workflow of your enterprise, automate the lion’s share of shop floor routine related to inventory handling, cut down on expenditures, and enhance the overall performance of the company.
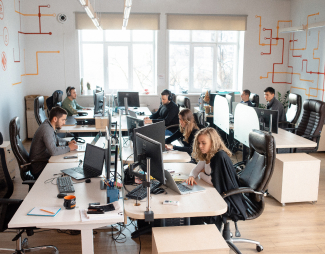
Our Engineers
Can Help
Are you ready to discover all benefits of running a business in the digital era?
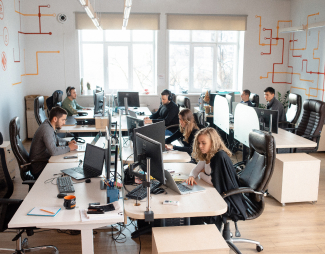
Our Engineers
Can Help
Are you ready to discover all benefits of running a business in the digital era?